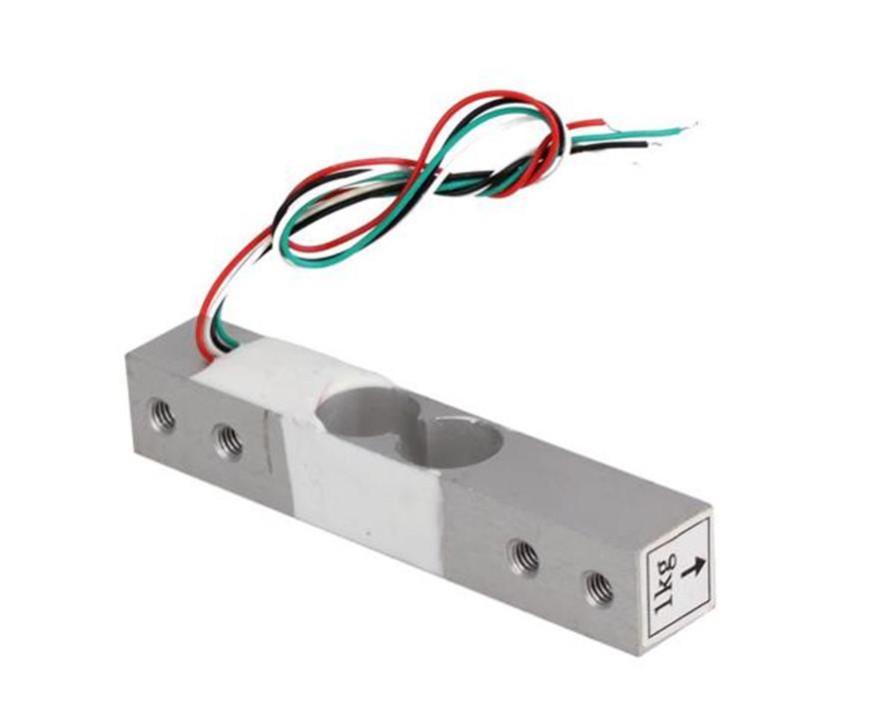
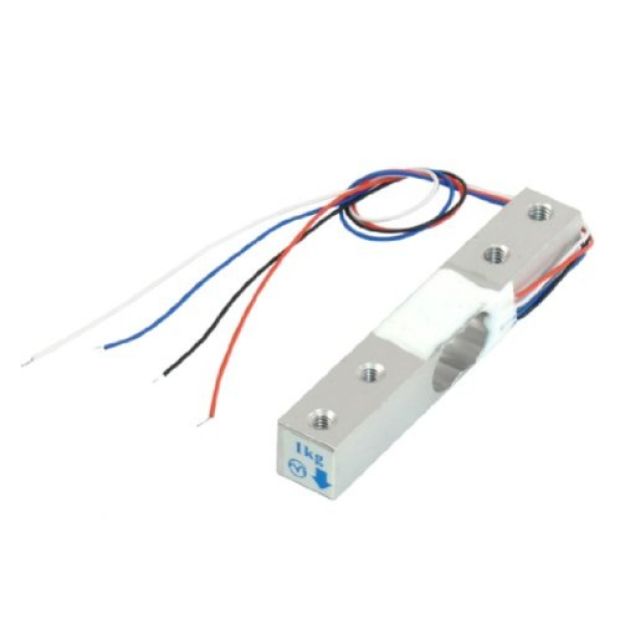
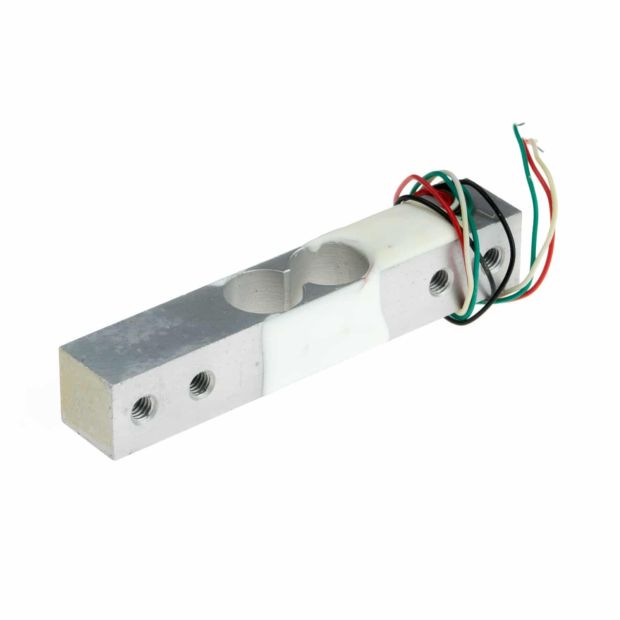
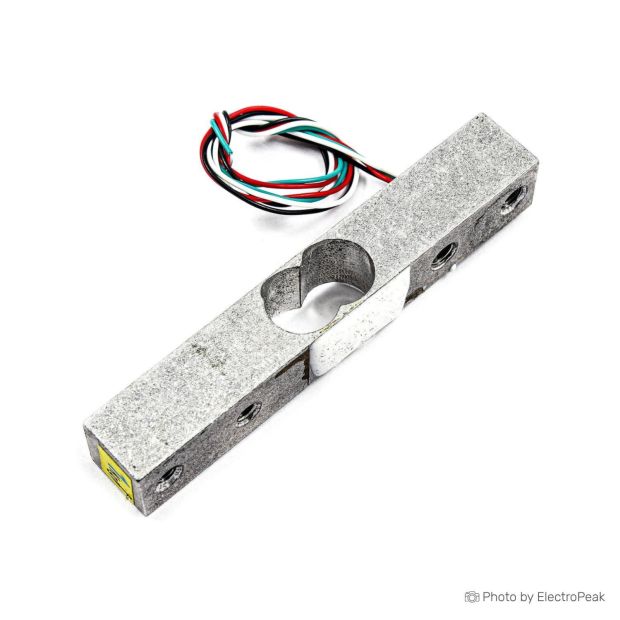
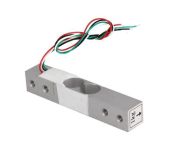
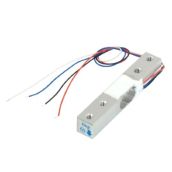
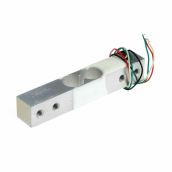
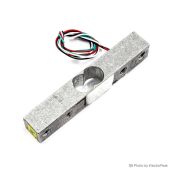
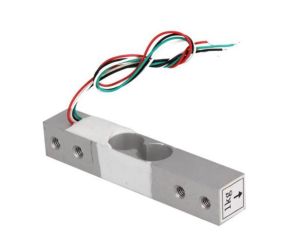
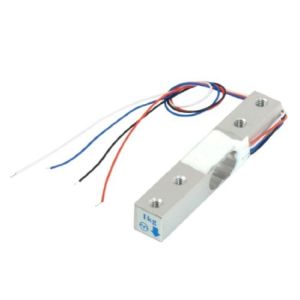
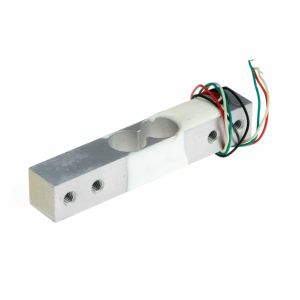
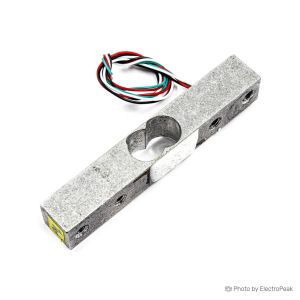
LOAD CELL 1KG
Each straight bar load cell is made from an aluminum-alloy and is capable of reading a capacity of 1kg. These load cells have four strain gauges that are hooked up in a wheatstone bridge formation. The color code on the wiring is as follows: red = E+, green = O+, black = E-, and white = O-
₹ 104 ₹149
149
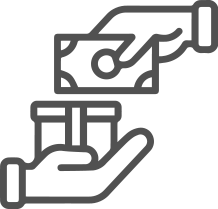
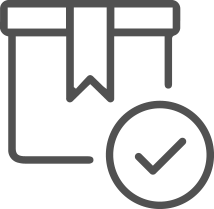
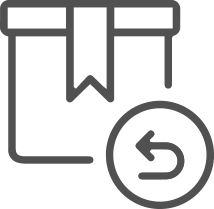
Made In : | India |
Add FAQ
A 1 kg load cell is a type of sensor used to measure force or weight. It’s a crucial component in various applications such as weighing scales, force measurement systems, and load testing. Here's a detailed overview:
Components and Functionality:
-
Strain Gauges:
- Strain Gauges: A load cell typically contains strain gauges that deform when a load is applied. These gauges are bonded to a metal structure and measure the strain (deformation) caused by the applied force.
- Wheatstone Bridge: The strain gauges are arranged in a Wheatstone bridge configuration to convert the small changes in resistance into a measurable electrical signal.
-
Metallic Structure:
- Load Cell Body: The body of the load cell is often made of materials like aluminum or stainless steel, which is designed to flex slightly under load, allowing the strain gauges to measure the deformation accurately.
-
Output Signal:
- Analog Output: The load cell produces a small analog voltage signal proportional to the applied load. This signal is typically in the millivolt range and needs amplification.
- Digital Output: Some load cells come with built-in analog-to-digital converters (ADCs) and provide a digital output, which can be directly interfaced with microcontrollers or digital systems.
-
Amplifier:
- Signal Conditioning: The raw signal from the load cell is very weak, so it requires amplification and signal conditioning to make it usable for measurement and control systems. Often, this is done with an amplifier circuit or a dedicated load cell interface module.
Specifications:
- Capacity: 1 kg (kilogram) or 10 N (Newton) for a 1 kg load cell.
- Accuracy: The accuracy of the load cell is often specified as a percentage of its full scale, such as ±0.1% FS (Full Scale).
- Output Sensitivity: The output sensitivity is usually given in mV/V, meaning how many millivolts are output per volt of excitation voltage applied.
Applications:
- Weighing Scales: Used in digital kitchen scales, laboratory balances, and industrial weighing systems.
- Force Measurement: In testing systems for measuring forces in materials or components.
- Robotics: For measuring force or weight in robotic applications and load monitoring.
- Load Testing: For determining the load-bearing capacity of structures or components.
Connecting a Load Cell:
-
Wiring:
- Excitation Wires: Typically, there are wires for excitation voltage (often labeled E+ and E-).
- Signal Wires: Wires for the signal output (often labeled S+ and S-).
- Shielding: To minimize noise interference, proper shielding and grounding practices should be followed.
-
Amplifier/Controller:
- Connect the load cell to a load cell amplifier or a microcontroller with an integrated ADC for converting the analog signal to a digital format.
- Calibration: Proper calibration is essential to ensure accurate measurements. This involves comparing the output with known weights and adjusting the system accordingly.
Example Setup:
- Power Supply: Provide the load cell with an appropriate excitation voltage (commonly 5V or 10V).
- Signal Conditioning: Use a load cell amplifier (like the HX711) to amplify the signal and convert it into a format suitable for your measurement system.
- Calibration: Use known weights to calibrate the system, ensuring that the output accurately reflects the applied load.
If you need help with a specific project or have questions about integrating a 1 kg load cell into your system, feel free to ask!
0 Reviews For this Product
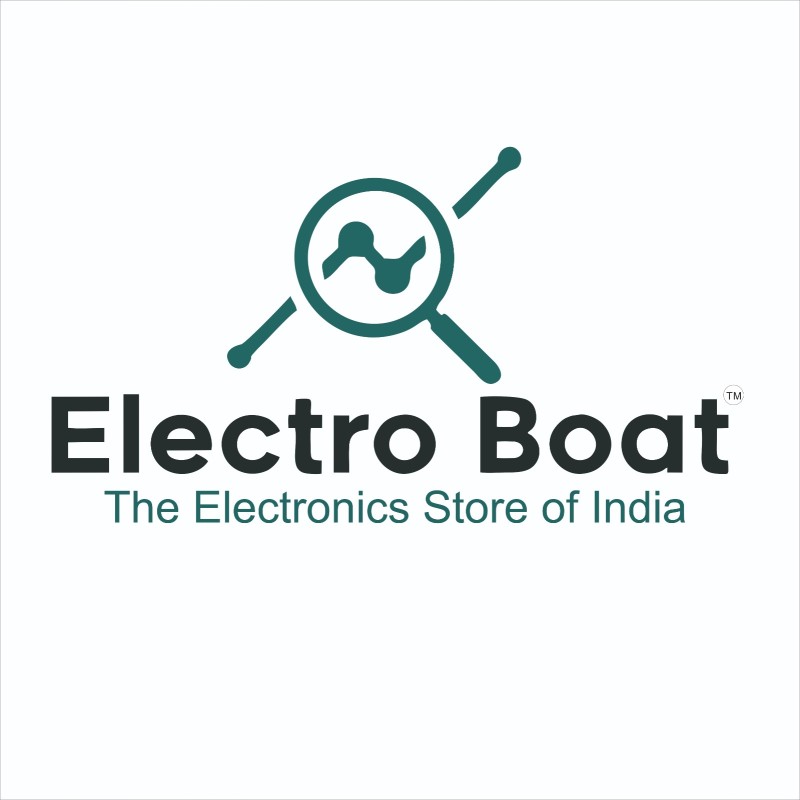