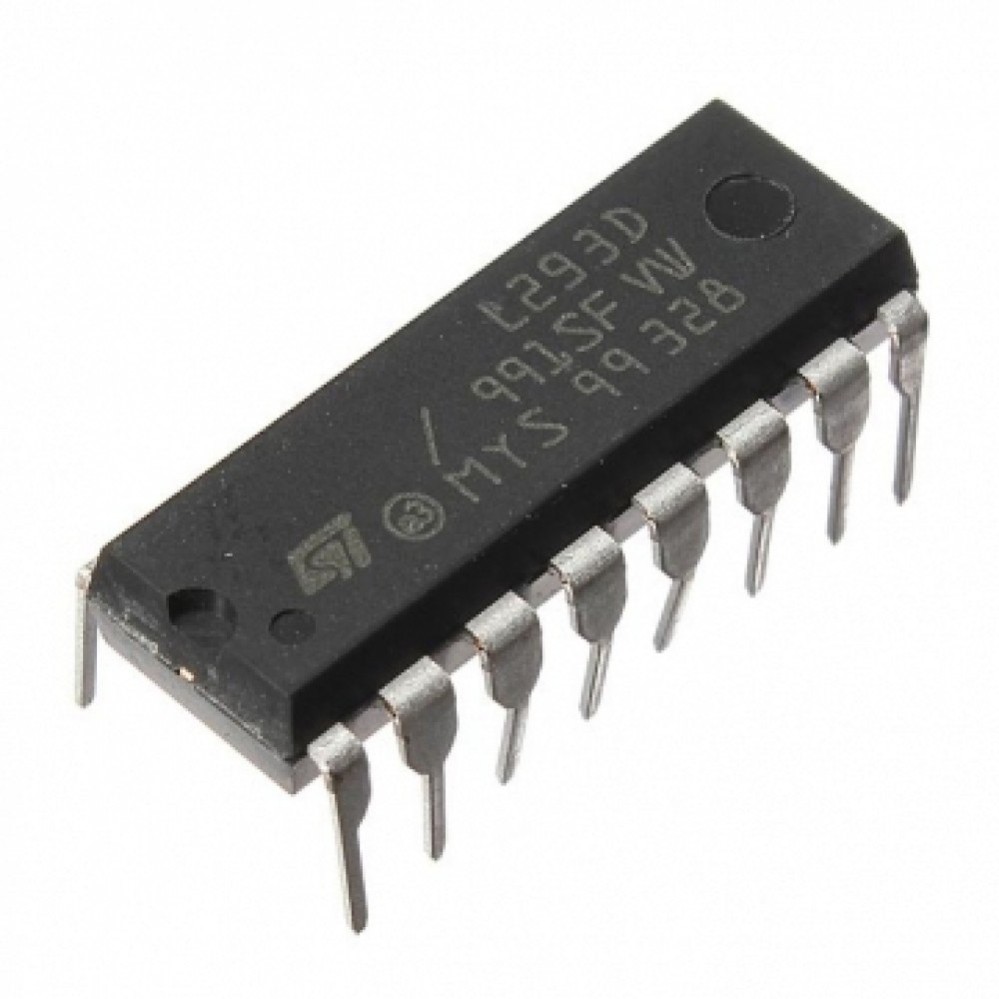
.jpeg&width=620&quality=80)
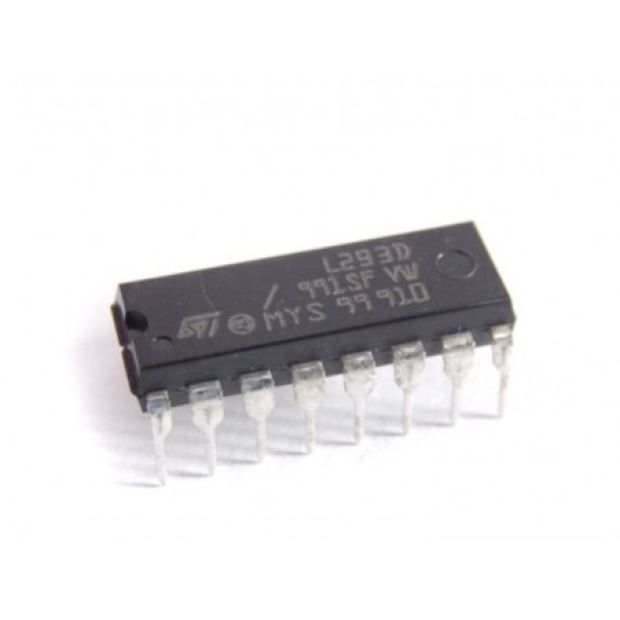
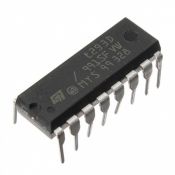
.jpeg&width=172&quality=80)
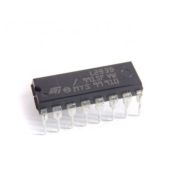
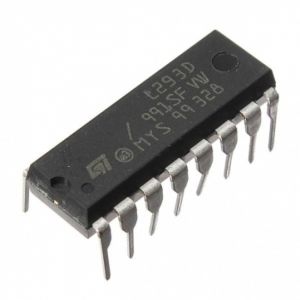
.jpeg&width=300&quality=80)
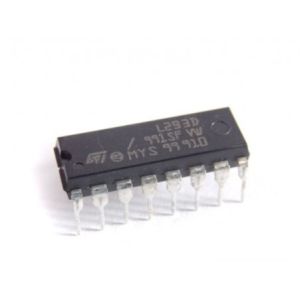
L293D IC
L293D is a basic motor driver integrated chip (IC) that enables us to drive a DC motor in either direction and also control the speed of the motor. The L293D is a 16 pin IC, with 8 pins on each side, allowing us to control the motor. It means that we can use a single L293D to run up to two DC motors.
₹ 36 ₹69
69
Add FAQ
The L293D IC is a popular motor driver integrated circuit used to control the direction and speed of DC motors and stepper motors. It is widely used in various applications such as robotics, automation, and motor control systems due to its simplicity and robustness.
L293D IC Overview
1. Key Features:
-
Dual H-Bridge:
- Contains two independent H-bridge circuits, allowing it to control two DC motors or one stepper motor.
-
Voltage Range:
- Input Voltage Range: Typically from 4.5V to 36V DC.
- Output Voltage Range: Up to 36V DC, matching the input voltage.
-
Current Capability:
- Continuous Output Current: Up to 600mA per channel.
- Peak Output Current: Up to 1.2A per channel for short durations.
-
Thermal Protection:
- Includes thermal shutdown and overload protection features to safeguard the IC from overheating and excessive current.
-
Built-in Flyback Diodes:
- Internal diodes protect the IC from back EMF generated by motors, which can otherwise cause damage.
2. Pin Configuration:
The L293D comes in a 16-pin Dual In-Line Package (DIP) or Surface-Mount Package (SMD). The pin configuration is as follows:
-
Pin 1 (Enable 1,2):
- Enables the H-bridge circuits for Motor 1. Connect this pin to a high logic level (e.g., 5V) to activate the motor.
-
Pin 2 (Input 1):
- Controls the direction of Motor 1. Setting this pin high or low will set the direction of the motor.
-
Pin 3 (Output 1):
- Connects to one terminal of Motor 1.
-
Pin 4 (GND):
- Ground pin. Connects to the ground of the power supply.
-
Pin 5 (Output 2):
- Connects to the other terminal of Motor 1.
-
Pin 6 (Input 2):
- Controls the direction of Motor 1, providing the opposite direction to Pin 2. Together with Pin 2, it determines the direction of Motor 1.
-
Pin 7 (VCC2):
- Connects to the power supply for the motors. This can be different from the logic power supply (VCC1).
-
Pin 8 (VCC1):
- Connects to the logic power supply (e.g., 5V), which powers the internal circuitry of the L293D.
-
Pin 9 (Enable 3,4):
- Enables the H-bridge circuits for Motor 2. Connect this pin to a high logic level to activate Motor 2.
-
Pin 10 (Input 3):
- Controls the direction of Motor 2. Setting this pin high or low will set the direction of Motor 2.
-
Pin 11 (Output 3):
- Connects to one terminal of Motor 2.
-
Pin 12 (GND):
- Ground pin. Connects to the ground of the power supply.
-
Pin 13 (Output 4):
- Connects to the other terminal of Motor 2.
-
Pin 14 (Input 4):
- Controls the direction of Motor 2, providing the opposite direction to Pin 10. Together with Pin 10, it determines the direction of Motor 2.
-
Pin 15 (VCC2):
- Connects to the power supply for the motors, similar to Pin 7.
-
Pin 16 (VCC1):
- Connects to the logic power supply, similar to Pin 8.
3. Working Principle:
-
H-Bridge Operation:
- The L293D IC uses H-bridge circuits to control the direction and speed of the motors. By changing the logic levels on the input pins, the H-bridge configuration determines the direction of current flow through the motor, thus controlling its rotation direction.
-
Motor Direction:
- Input pins (Input 1 and Input 2 for Motor 1; Input 3 and Input 4 for Motor 2) set the direction of the motors. For example, setting Input 1 high and Input 2 low will rotate Motor 1 in one direction, while reversing the logic levels will rotate it in the opposite direction.
-
Speed Control:
- Speed can be controlled using Pulse Width Modulation (PWM) applied to the enable pins (Enable 1,2 and Enable 3,4). By varying the duty cycle of the PWM signal, the effective voltage applied to the motor can be adjusted, thereby controlling the speed.
4. Applications:
-
Robotics:
- Used to control DC motors for movement, steering, and other functions in robots.
-
Automation:
- Controls motors in automated systems for applications such as conveyor belts, actuators, and more.
-
DIY Projects:
- Commonly used in hobbyist projects to drive small motors for various mechanical tasks.
-
Home Appliances:
- Integrated into household devices for motor control functions such as in washing machines and automated curtains.
5. Advantages:
-
Ease of Use:
- Simplifies motor control by integrating H-bridge circuitry and protection features into a single IC.
-
Built-in Protection:
- Includes thermal shutdown and back EMF protection, enhancing reliability and durability.
-
Versatility:
- Can control both DC motors and stepper motors, making it suitable for a range of applications.
6. Limitations:
-
Current Limitation:
- The maximum continuous current of 600mA per channel may not be sufficient for high-power motors.
-
Heat Dissipation:
- High current operation may require additional cooling or heat sinking to prevent overheating.
Example Use Case:
Robotic Car:
- In a robotic car, the L293D IC can be used to drive two DC motors for forward, backward, and turning movements. By controlling the input and enable pins with a microcontroller, the direction and speed of the motors can be precisely managed.
Summary:
The L293D IC is a versatile motor driver suitable for controlling DC motors and stepper motors in various applications. Its dual H-bridge design, built-in protection features, and ease of use make it a popular choice for robotics, automation, and hobbyist projects. By controlling the direction and speed of motors, the L293D enables precise and reliable motor control in electronic systems.

0 Reviews For this Product
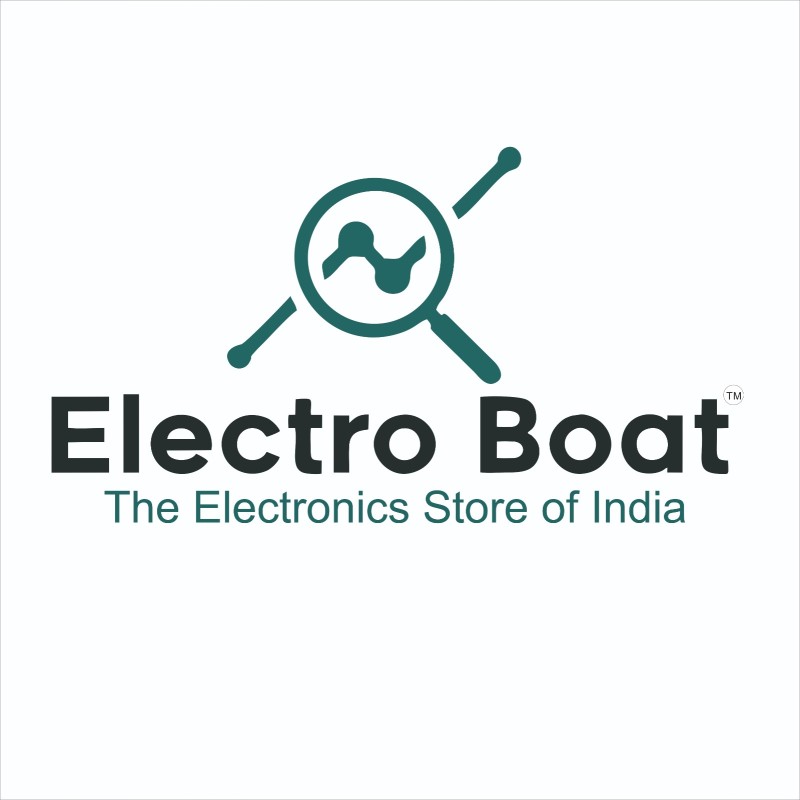